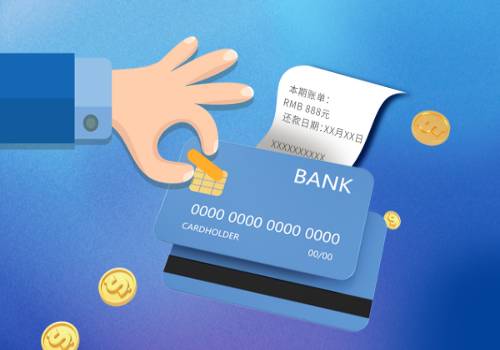
【资料图】
本发明公开了一种球化晶种合金及其制备方法,原料为5%~15%的Mg,20%~45%的Si,2%~8%的稀土,0.4%~2.8%的Te,余量为Fe和杂质,将Si-Fe、稀土S-iFe、废钢混合熔融之后加入碎块,搅拌均匀并除渣,随后加入Mg锭,待充分熔化搅拌后,冷却浇注成形。该方法可以增加球Fe石墨球的数量,改善球化质量。
2020年中国球墨铸铁产量1500余万吨,而作为生产球墨铸铁必不可少的球化剂在其生产中尤为重要。球化剂中起关键因素为球化元素,球化元素与铁水中S、O等元素的亲和力强,提高铁水的表面张力,从而使石墨形态由片状变为球状。
目前球化元素主要为镁与稀土。镁加入铁水时,可以产生汽化,使铁水翻腾,且与S、O有很强的亲和力,Mg处理后的铁水,S、O含量都很低。当其在铁水中的残留量超过0.035%时,石墨就可以球化。Re:稀土族元素对石墨球化有显著作用Ce和Y,其具有比Mg更强的脱硫脱氧能力,含稀土的球化剂比镁球化剂的抗干扰能力强。稀土元素残留量对石墨球化有明显的影响。当残留稀土含量0.04%时,石墨可以球化,而且很稳定。
为使球化剂反应平稳,通常用钙和镁、稀土混配,使球化处理平稳,还可以减少因稀土造成的较大白口倾向。上球化剂中的球化元素(镁与稀土)与铁水中硫、氧等元素的亲和力强,提高铁水的表面张力,最终石墨形成球状。反球化元素要么消耗球化元素,要么降低铁水表面张力,因此球化剂中是严禁含有反球化元素的。目前,急需研发一种新型的球化剂以满足现有生产。
表1 实施例与对比例球化率及石墨个数密度对比表
在针对石墨球结构的研究中发现,石墨不是纯碳构成,而是在石墨球中心或近中心有夹杂物,这些夹杂物可以吸附碳,而作为石墨形核核心。并在试验中发现,球化元素中的稀土与反球化元素中的Te以合金的形式组合可以提供意想不到的一种石墨形核核心(ReTe/Re2Te3)。该晶种可促进石墨形核与球化石墨,用于球墨铸铁铸造。
本发明所述的晶种球化剂中合金可以增加球铁石墨球的数量,改善球化质量。合金中的Te与金属结合,以化合物而非单质状态存在,不仅不会干扰球化,反而均匀分布与铁水中,首要功能是能够起到石墨形核核心的作用。低密度的碲化物与其他夹杂物,例如氧化镁、硫化铁等在球化时会随着渣子上浮,并被清除。
免责声明:本文原创自专利局正式授权发表专利,仅供学术交流,数据和图片来源于所属专利局,如有侵权请联系删除。
标签: